Silicone rubber keypads are a commonly used button material that offers a soft touch and excellent wear resistance. They are created through a drop molding process, where silicone material is dropped onto the button's surface to form a uniform silicone film. This process not only ensures a comfortable button experience but also enhances the button's waterproof and dustproof capabilities.
Silicone rubber keypads find extensive applications in electronic products, communication devices, automobiles, and various other fields, offering users reliable performance and convenient operation. The process of manufacturing silicone buttons involves several steps.
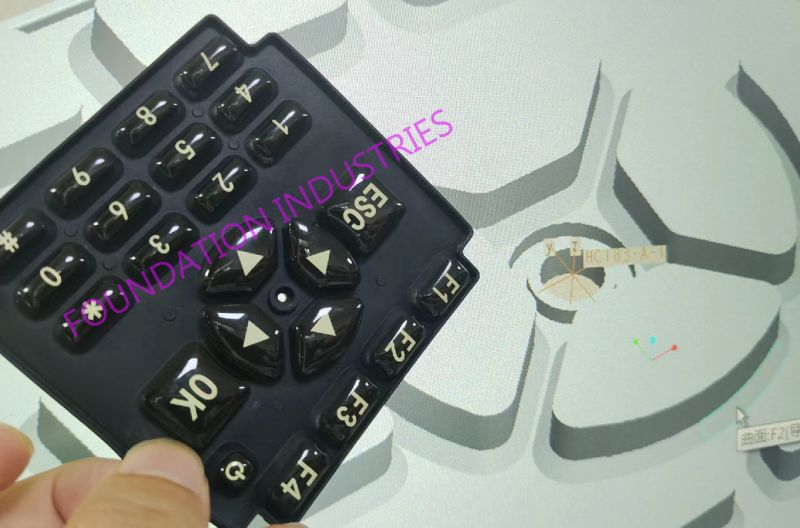
Firstly: Suitable silicone materials, such as silicone rubber and silicone coating, are prepared. Secondly: Molds for the silicone buttons are created based on design requirements, which can be made of metal or silicone.
Thirdly: The silicone material is applied to the mold's surface to ensure an even coating.
Fourthly: The coated mold is placed in a curing device for the necessary curing treatment, with the curing time and temperature controlled according to the silicone material's specifications. Once the silicone buttons are cured, they are removed from the mold.
Finally: The buttons are inspected to ensure they meet quality requirements, and if necessary, trimming can be performed, such as adjusting the shape or trimming the edges.
The epoxy drop process of silicone buttons involves using a drop molding machine to drop silicone material onto the button's surface, resulting in a uniform silicone film. This process imparts a soft touch and excellent wear resistance to the buttons, while also providing waterproof and dustproof functions.
Silicone buttons are widely utilized in electronic products, communication devices, automobiles, and other industries, offering a comfortable button experience and reliable performance.
Post time: Oct-30-2023