The membrane circuit is an emerging electronic technology that offers numerous advantages. It enables high-density circuit wiring, resulting in more compact and lightweight electronic devices. Additionally, the membrane circuit is flexible and bendable, allowing it to adapt to different shapes and sizes of devices. It also boasts lower power consumption and higher reliability, ensuring stable circuit connection and transmission performance. As a result, the membrane circuit finds wide application in electronic products like smartphones, tablets, and wearable devices.
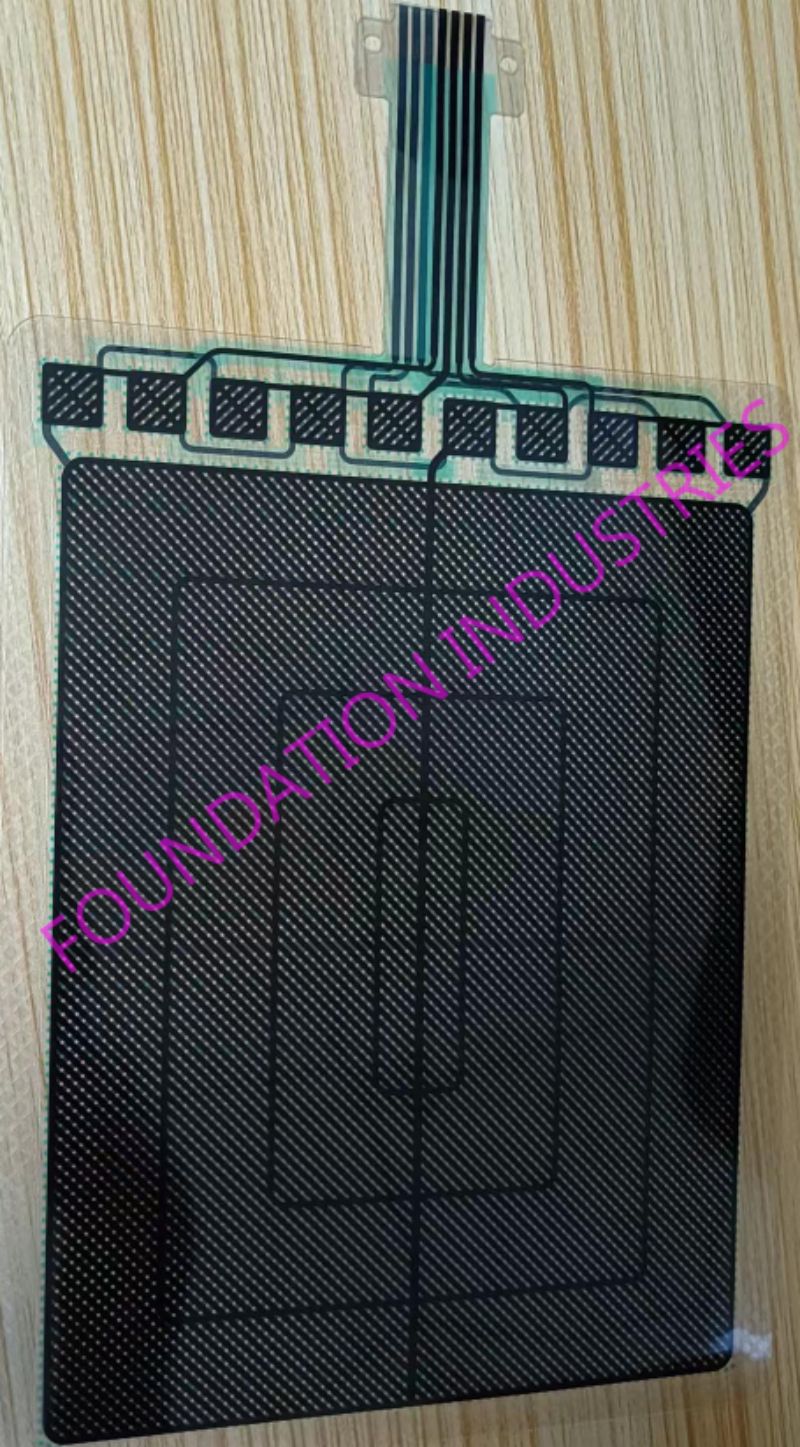
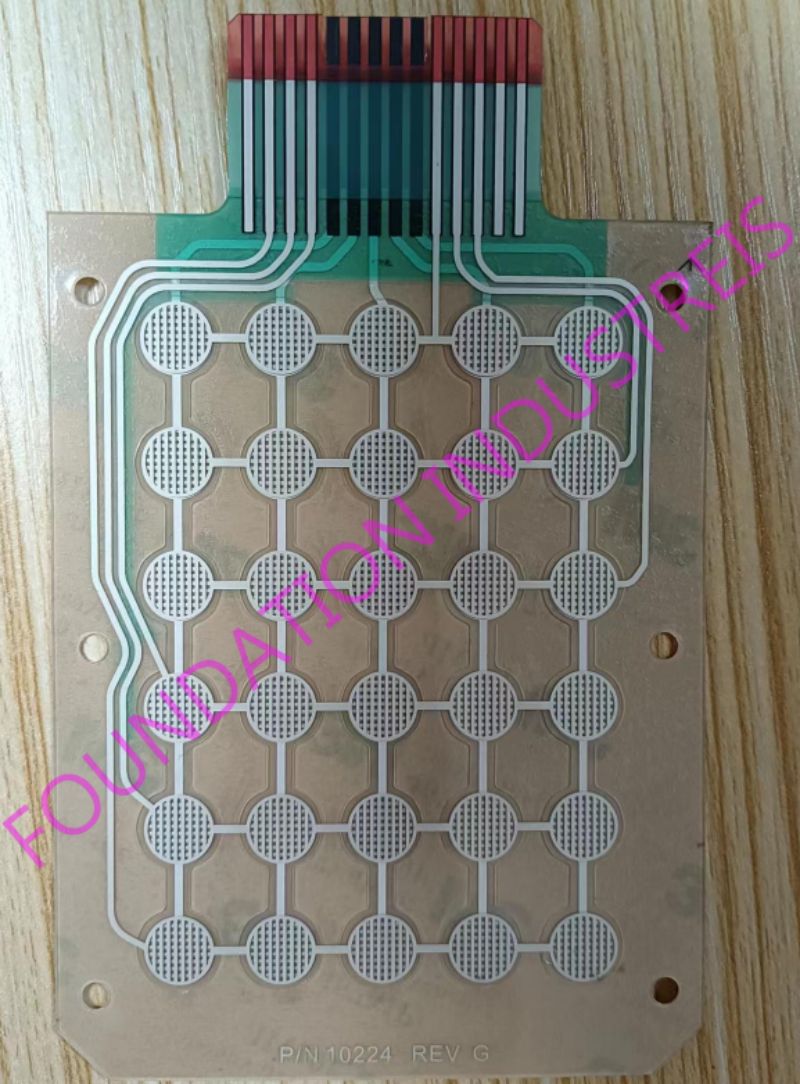
The process of creating membrane switches involves using thin film materials. These switches are electronic switches that utilize thin film materials as triggers to open or close circuits through pressure or deformation. The manufacturing process of membrane switches includes the following steps:
1. Material selection: Choose suitable thin film materials, such as polyester film or polyimide film, considering the switch's operating environment and requirements.
2. Thin film fabrication: Cut and process the selected thin film materials to create membrane film shapes and sizes that meet the design requirements.
3. Circuit printing: Use printing techniques, like screen printing or inkjet printing, to print circuit patterns on the membrane film, forming conductive circuits.
4. Trigger fabrication: Create triggers on the thin film in accordance with the design requirements. This is usually achieved by sticking together layers of double-sided adhesive, which allows for the assembly of components on the membrane circuit while keeping the adhesive layer keep away from.
5. Packaging and connection: Package the fabricated thin film switch, securing it to a base and connecting it with other electronic components using adhesive or heat pressing techniques.
As technology continues to advance, the process of membrane switches is also constantly evolving and improving to meet the ever-changing demands of the market.
Post time: Nov-01-2023